Each
business day many companies throw away a valuable corporate asset, the
history of production. The PI System fully automates the collection,
archiving
and dissemination of this information.
Process
and plant data are the foundation of many business decisions. This
information
must be available to everyone, unfiltered and when needed. The PI
System
provides a fully automated package to collect, store, present and
distribute
plant data. Convenient and fast data access can significantly reduce
the
time required to make critical quality, cost, safety and environmental
decisions. The direct access to validated and timely plant information
also improves decision-making and performance. The PI System by OSI
Software
makes all this happen in a wide range of industries, every day.
PI has
the largest installed base of any Plant Information Management System.
The PI System features an open client/server architecture that delivers
data to the desktop, while preserving data security. The PI System Data
Archive stores all the plant data on-line for years, and a wide variety
of tools for exchanging data with other systems are supported. Whether
you call it a Millwide Information System, a Refinery Information
Management
System, a Plantwide System, MES, or enterprise-wide computing, PI is an
enterprise wise way to gain process knowledge; one that is remarkable
easy
to use, implement and manage.
Hundreds
of companies worldwide rely on the PI System for continuous improvement
of plant performance, product quality and customer service. To replace
a legacy system, build a new plant information system, or integrate a
variety
of process software applications, the PI System is the answer.
In today's
competitive environment, manufacturers are expected to make higher
quality
products with faster delivery, lower prices, fewer emissions and less
waste.
Here are some examples of how companies are using the PI System to meet
these increasingly difficult demands:-
Lower
Productions Costs
The
PI System's data analysis and graphical tools permit problems to be
resolved
faster, and often prevent small conditions from becoming major upsets.
Many companies report that the data stored in PI allow them to improve
their preventive maintenance programs, increasing equipment life. These
uses result in increased production and lower operating costs. In
addition,
the PI System contributes to yield improvements and less waste. When
the
lab system sends messages to operations via the PI System, for example,
the time required to change grades decreases, increasing production and
minimizing waste.
Higher
Product Quality
The
time to respond to a quality problem is before the product goes out of
spec. Applications such as the PI-Profiles package allow
inconsistencies
to be noticed and fixed before they become serious problems. Operators
also appreciate the PI System because they can review operating
conditions
from previous runs, a valued feature when producing unusual or
difficult
product grades. The PI System provides an easy-to-use mechanism for
obtaining
and monitoring continuous process improvement. These programs
frequently
lead to improved product quality with no increases in production costs.
Better
Customer Service
With
access to a PI System, customer service and quality assurance groups
can
quickly respond to customer complaints and concerns about product
quality.
This is because process data are stored at high resolution and remain
on-line
for extended periods of time. Personnel are also able to analyze past
data
to determine whether requests for new grades or product specs are
feasible.
And, because current data are also available, sales teams can review
process
conditions to determine when a new order can be scheduled or delivered.
Increased
Productivity and Improved Process Knowledge
Less
time is wasted trying to obtain data and information relating to a
problem,
so more time is available for solving it. Everyone throughout the
facility
uses a common set of data, eliminating discussions of whose data set is
"right", again contributing to a more productive use of everyone's
time.
Also, applications developed internally with the PI System, such as
performance
monitoring and efficiency calculations may be shared between sites,
reducing
development time.
Simplified
Environmental Reporting
Having
one system containing all the process data from a facility makes it
easier
to comply with environmental, health and safety regulations. In
addition,
the calculations enable inferred values to be used in lieu of
unreliable
measurement points. PI System users are able to meet many of these ever
changing requirements with a package that also helps them improve their
process and lower their costs.
|
|
The
PI SystemTM is a client/server based software program
designed to fully automate the collection, storage and presentation of
manufacturing plant data. PI employs a flexible architecture that can
be
implemented in a variety of system configurations.
The PI
Data Server provides centralized collection of information, a real-time
database and a historical data archive. PI client software packages put
the maximum amount of information processing power possible in the
hands
of the user. These clients, which include PI-DataLinkTM
and PI-ProcessBook®, allow the user to work in
the
familiar Microsoft® WindowsTM
environment.
Each
PI System can interface to one or more real-time systems simultaneously
and can read and write to virtually any real-time device or database.
Integration
tools, which include ActiveX controls, ODBC, and a large set of
application
programming interfaces, can be employed over the internet or in more
traditional
programming environments.
PI-ProcessBook®
Real-time
and/or historical plant data can be displayed in PI-ProcessBook by
creating
process graphics, trends, statistical plots and tables. PI-ProcessBook
is an ActiveX control container, features embedded Visual Basic for
Applications
(VBA) and is an ODBC container that enables users to easily combine
data
from PI and other databases on the same trend or display.
PI-ProcessBook
is an ideal platform for integration efforts. Data may be displayed in
a variety of formats, including process graphics, trends, statistical
plots,
tables and charts. Displays are easy to configure and may be created in
advance or built as desired. The same displays may be used for current
or historical data, and may be accessed by anyone connected to the
plant
network via PCs or workstations.
PI-DataLinkTM
PI-DataLink
provides an easy-to-use live link between the PI System and
spreadsheets.
The PI-DataLink add-in provides pull-down menu functions for accessing
real-time or historical data. PI-DataLink is a popular way to create
production
reports and to analyze process data. Users do not need to login to the
server and no special procedures are required. Add-in functions and
dialogue
boxes allow users to quickly access real time or historical data.
Customers
continue to use previously configured spreadsheets, but no longer need
to input data or use complex data import procedures.
PI-BatchViewTM
PI-BatchView
is a client application that allows PI customers to view data from a
batch-oriented
perspective. The PI-BatchView add-in to PI-ProcessBook supports
trending
data by batch; and the PI-DataLink add-in enables spreadsheet analysis
by unit, product and Batch ID.
PI-ActiveViewTM
PI-ActiveView
brings your PI-ProcessBook applications to the web. PI-ProcessBook
displays
run without modification because PI-ActiveView uses Microsoft's Visual
Basic for Applications and can take advantage of embedded ActiveX
controls.
PI-Data
ArchiveTM
PI
Systems
are designed to accommodate very large real-time and historical
databases,
with every process point stored on-line for years, to very near its
original
resolution. Plant or corporate-wide PI Systems can employ multiple data
archives. Data archives can be implemented in different system sizes
ranging
from 1,000 tags to over 100,000 tags.
PI-ODBC
PI-ODBC
makes the PI-Data Archive appear and act like a set of relational
tables.
PI-ODBC is frequently used to supply summary data such as Averages,
Minimums,
Maximums and Totals. Retrieval is very fast and the hazards of data
duplication
are eliminated.
PI
System Interfaces
The
data stored in PI can be generated by Distributed Control Systems
(DCS),
Programmable Logic Controllers (PLC), Lab Systems, SCADA Systems, via
manual
recording and by numerous other sources. Over 300 interfaces to common
information systems are available to transfer data to and from PI. A
single
PI System can include many interfaces, permitting data from several
control
systems or process areas to be combined and available throughout the
facility.
Sigmafine
Sigmafine has
been
licensed to over 100 sites worldwide. Many technologies and methods are
required to properly generate a set of reconciled data for a process
plant.
The knowledge from development and installation process of previous
Sigmafine
sites is used for continuous improvement.
An accurate
source of information
is essential to the profitability of a process plant. Plant data is the
basis for any form of numerical analysis. With the increasing use of
automation,
operational data becomes much more accessible to the users. However,
this
data is commonly imperfect. It often shows little consistency between
different
process units. Missing product flows, unaccounted material losses and
equipment
down time, reflect gross metering errors.
Sigmafine
represents a new-generation
Windows-based data reconciliation and yield accounting application. It
allows the site to more accurately analyze the quality of flow and
inventory
measurements and produce a single consistent set of the most accurate
reconciled
data possible.
For more product information and downloads
Contact
us today
TEKNIK
SEGALA SDN BHD
No
32
Jalan Bandar 13, Pusat Bandar Puchong
47160
Puchong, Selangor, MALAYSIA
Tel: +60 (03) 5882 6777 Fax: +60 1700 810 533

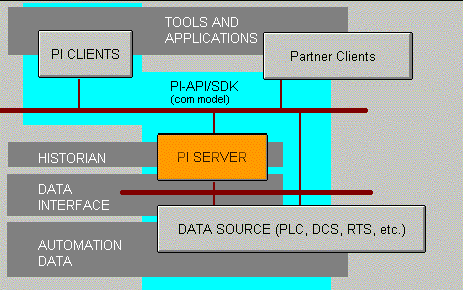
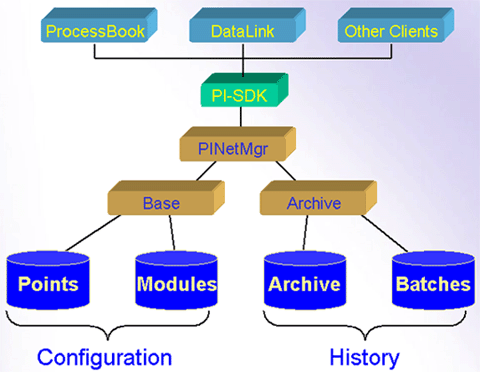
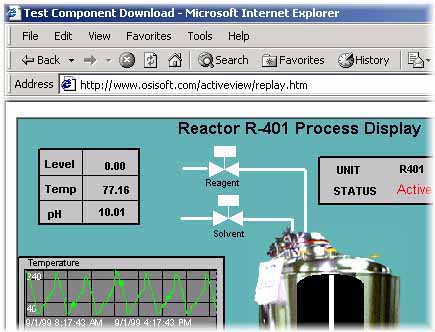
|